Key Benefits of GenAI in Additive Manufacturing
BeginnerGenerative AI technologies are revolutionizing additive manufacturing across the entire production lifecycle. By combining the design freedom of AM with the creative and optimization capabilities of AI, manufacturers can achieve outcomes that were previously impossible or impractical.
Primary Benefits:
- Enhanced Design Capabilities: Creation of complex, optimized structures beyond human design capacity
- Process Efficiency: Streamlined workflows and reduced trial-and-error through intelligent parameter selection
- Quality Improvements: Better defect detection and prevention through AI-powered monitoring systems
- Cost Reduction: Lower material usage, reduced waste, and shorter development cycles
- Expanded Application Range: Enabling new use cases by overcoming traditional AM limitations
These benefits are transforming how manufacturers approach product development, prototyping, and production, creating new possibilities for innovation and efficiency.
Design Optimization
BeginnerGenerative AI enables remarkable advances in product design for additive manufacturing, creating optimized structures that would be impossible to conceive through traditional design methods.
AI-generated lattice structure optimized for weight reduction while maintaining structural integrity
Key Design Benefits
Topology Optimization
GenAI can create structures that achieve maximum strength with minimal material usage by intelligently distributing material only where needed.
The algorithm considers:
- Load conditions and constraints
- Manufacturing limitations
- Material properties
- Functional requirements
Generative Design Exploration
AI systems can rapidly explore thousands of design variations to identify optimal solutions that human designers might never consider.
Benefits include:
- 30-50% weight reduction in many applications
- Improved performance characteristics
- Consolidation of multiple parts into single components
- Material-efficient internal structures (lattices, honeycombs, etc.)
Example: Aerospace Bracket Redesign
A traditional aerospace mounting bracket was redesigned using generative AI techniques. The resulting design:
- Reduced weight by 35% while maintaining all strength requirements
- Simplified the assembly by consolidating 5 separate components into a single part
- Optimized internal lattice structures for vibration dampening
- Reduced material usage and associated costs by 40%
Process Parameter Optimization
IntermediateOne of the most significant challenges in additive manufacturing is selecting optimal process parameters. Generative AI systems can predict and optimize these parameters, dramatically reducing the traditional trial-and-error approach.
Parameter Prediction and Optimization
GenAI models can analyze and optimize parameters such as:
- Laser Power and Speed: For powder bed fusion processes
- Layer Height and Extrusion Settings: For material extrusion
- Build Orientation: For optimal part strength and surface finish
- Support Structure Generation: Minimizing supports while ensuring buildability
- Slicing Parameters: Infill patterns, densities, and toolpath strategies
AI system predicting optimal process parameters based on part geometry and material properties
Simulation Integration
Advanced GenAI approaches combine machine learning with physics-based simulations to predict:
- Thermal distribution during printing
- Residual stress development
- Potential distortion and warping
- Microstructure formation
# AI-driven parameter optimization pipeline
from am_optimization import ParameterOptimizer, Material, Geometry
# Initialize with part geometry and material
optimizer = ParameterOptimizer(
geometry=Geometry.from_stl("part.stl"),
material=Material.TITANIUM_TI64,
process=ProcessType.POWDER_BED_FUSION,
machine=Machine.EOS_M290
)
# Define optimization objectives
optimizer.set_objectives(
minimize_material_usage=True,
minimize_build_time=True,
maximize_surface_quality=True,
weight_factors=[0.3, 0.3, 0.4]
)
# Set constraints
optimizer.set_constraints(
min_feature_size=0.5, # mm
max_overhang_angle=45, # degrees
max_residual_stress=500 # MPa
)
# Run optimization
optimal_params = optimizer.optimize(
population_size=100,
generations=50,
simulation_fidelity="high"
)
print(f"Optimal parameters found: {optimal_params}")
Business Impact
The benefits of AI-driven process parameter optimization include:
- Reduction in Build Failures: Typically 30-60% fewer failed builds
- Material Savings: 15-25% reduction in material usage through optimized parameters
- Time Savings: 40-70% reduced development time compared to traditional trial-and-error
- Consistent Quality: More repeatable results across builds and machines
Defect Detection and Quality Control
IntermediateGenerative AI is revolutionizing quality control in additive manufacturing through advanced defect detection, prediction, and prevention systems. These technologies enable real-time monitoring and adjustment, significantly improving part quality and process reliability.
Real-Time Monitoring
AI-powered computer vision systems can monitor the building process layer-by-layer, identifying defects as they occur:
- Porosity and void formation
- Layer delamination
- Surface irregularities
- Powder bed anomalies
- Thermal anomalies
These systems can achieve detection rates of 95%+ for common defect types, far exceeding human inspection capabilities.
Predictive Quality Assurance
Beyond detection, advanced GenAI models can predict potential defects before they occur by analyzing:
- Part geometry and orientation
- Process parameters and their interactions
- Material properties and batch variations
- Environmental conditions
- Historical build data
This predictive capability enables proactive adjustments to prevent defects rather than simply detecting them.
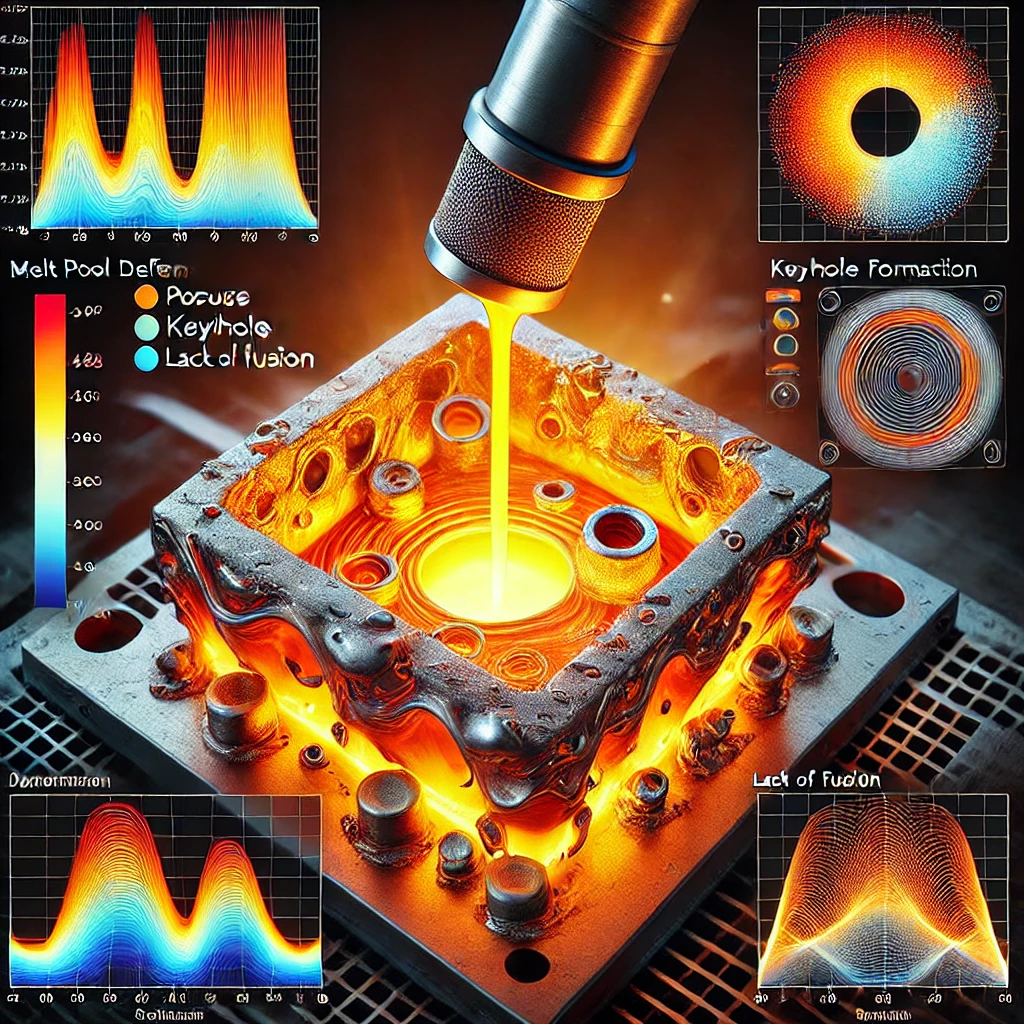
AI system detecting and classifying defects in real-time during a powder bed fusion process
Closed-Loop Control
The most advanced implementations combine defect detection with automatic process adjustment:
- Detection: AI identifies developing anomalies or potential issues
- Analysis: The system determines the root cause and potential remediation
- Adjustment: Process parameters are automatically modified to address the issue
- Verification: The system confirms the adjustment resolved the problem
- Documentation: All interventions are logged for quality assurance
Example: Medical Device Manufacturing
A manufacturer of custom medical implants implemented an AI-based quality control system with the following results:
- 73% reduction in post-production rejection rate
- Real-time detection of critical defects with 98.7% accuracy
- Automatic adjustment of laser parameters when thermal anomalies were detected
- Complete digital thread documentation for regulatory compliance
- ROI achieved within 8 months through reduced waste and rework
Business Benefits and ROI
AdvancedBeyond the technical advantages, implementing generative AI in additive manufacturing delivers significant business benefits and competitive advantages. Understanding these benefits helps build the business case for GenAI adoption.
Quantifiable Business Benefits
Benefit Category | Typical Improvement | Impact Areas |
---|---|---|
Development Time | 40-70% reduction | Faster time-to-market, reduced engineering costs |
Material Efficiency | 20-45% improvement | Lower material costs, reduced environmental impact |
Part Performance | 15-35% improvement | Enhanced product capabilities, competitive advantage |
Quality Consistency | 50-80% fewer defects | Reduced waste, higher customer satisfaction |
Production Flexibility | 3-5× faster adaptation | Ability to quickly respond to market changes |
Strategic Advantages
- Intellectual Property Generation: AI-generated designs can lead to patentable innovations
- Mass Customization: Efficient production of customized products at near-mass production economics
- Supply Chain Resilience: On-demand production capabilities reduce dependency on complex supply chains
- Sustainability: Improved material efficiency and optimized designs reduce environmental footprint
- Digital Transformation: Catalyst for broader digital manufacturing integration
Implementation ROI Timeline
Based on industry benchmarks, GenAI implementations in AM typically demonstrate the following ROI progression:
Initial Implementation
Focus on training, integration, and proof of concept applications. Limited measurable returns during this phase as systems are calibrated and workflows established.
Early Benefits
First measurable improvements in design efficiency and material usage. Typical ROI metrics show 10-20% improvements in targeted processes.
Positive ROI
Break-even point typically reached. Expanded application across more products and processes. Data feedback loops improve AI performance.
Maximum Value
Full integration into workflows and product lifecycle. Development of company-specific AI capabilities. Strategic advantages realized in market position.
Challenges & Considerations
AdvancedWhile the benefits of GenAI in additive manufacturing are substantial, there are important challenges and considerations that organizations should address when implementing these technologies.
Technical Challenges
- Data Requirements: Many GenAI approaches require substantial training data which may not be readily available in AM contexts
- Simulation Fidelity: Balancing computational efficiency with prediction accuracy in process simulations
- Interoperability: Ensuring AI systems can integrate with existing CAD, CAM, and MES systems
- Validation Methodologies: Establishing reliable approaches to validate AI-generated designs and parameters
Business Considerations
- Implementation Costs: Including technology, training, and workflow adjustments
- Skill Requirements: Need for specialized expertise in both AM and AI domains
- Intellectual Property: Questions around ownership of AI-generated designs
- Risk Management: Establishing appropriate oversight and validation processes for AI systems
Mitigation Strategies
Organizations can address these challenges through several approaches:
- Staged Implementation: Begin with well-defined, high-value applications before broader deployment
- Cross-Functional Teams: Combine AM expertise with AI/ML knowledge for effective implementation
- Transfer Learning: Leverage pre-trained models to reduce data requirements for specific applications
- Clear Governance: Establish protocols for design validation, testing, and quality assurance
- Continuous Learning: Implement systems that improve over time with operational feedback
Ready to Explore GenAI Benefits in Your AM Operations?
Learn how to implement these technologies in your specific context with our practical resources: